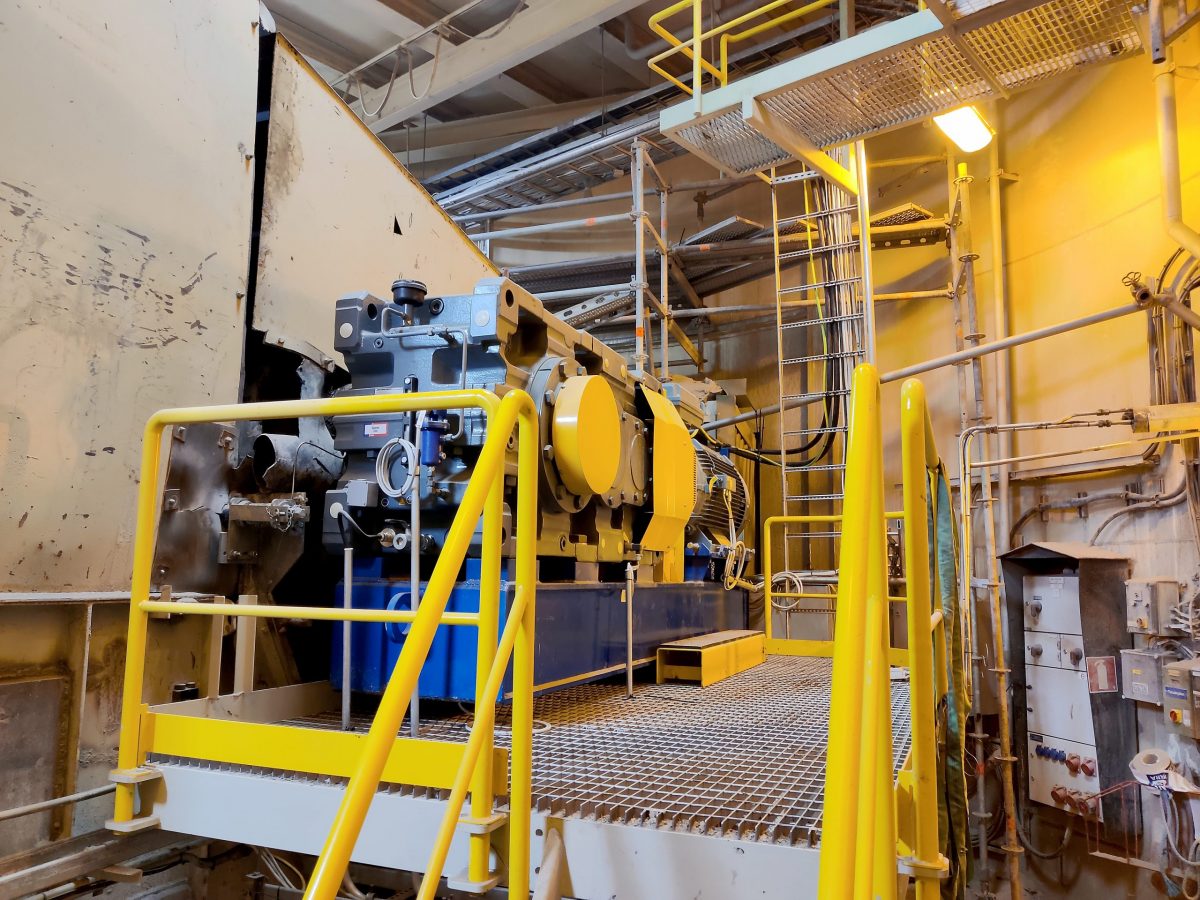
Simetek modernises the largest conveyor at Yara’s mine area
A KA1160 conveyor deployed in the late 1970s at Yara’s Siilinjärvi mine required modernisation as it was still using the original drive gears and power industrial gearbox. Simetek Works implemented a modernisation project from mechanical engineering to installation.
The KA1160 transports crushed stone from the gyratory crusher to a day silo, from where it is transported using a conveyor to a fine crusher. The conveyor lifts material a total of 75m from below ground to the top of the silo and transports it a length of 390 metres. The conveyor capacity is 2000 tonnes per hour.
“This is our production plant’s largest conveyor, and from a technical standpoint, it is a demanding project with its dual use. It was nice to see that a local service provider was able to offer and implement a functional solution,” says Yara’s maintenance manager Anssi Pietarinen.
The conveyor’s pulley drive was modernised, in practice by adding two new gears and new beds for the gears and electric motor. Alongside another gearbox, a maintenance platform was also manufactured to make maintenance easier.
“Planning the modernisation required strength calculations and the redimensioning of the gears in order for the conveyor to be able to withstand the current load, and a possible increase in capacity. Before planning, the conveyor’s pulley was laser scanned so that we could use the scanning data to design modification drawings,” says design manager Pasi Knuuttila from Simetek.
Installation was carried out on a tight schedule
Simetek designer Matti Hirvonen designed the new components for the pulley and also acted as installation foreman in the project.
“I was able to make quick decisions during the installation phase as I acted both as designer and installation foreman. I knew what the next work phase was without looking at the images. I also knew the dimensions off by heart, which meant that the installation moved swiftly forward,” says Hirvonen.
Good preparation is key to the success of an installation. Hirvonen gathered all of the required supplies in the week prior to the installation, so there were no unnecessary trips to the machine shop to pick up components.
The installation also required a tight schedule. The old equipment had to be disassembled and new ones installed in the space within a week. Hirvonen is grateful for the good work group involved in the installation. There was a good atmosphere in the installation team, and we were all left with a positive impression.
“I was tightening bolts and acting as a hot work guard just like everyone else. I didn’t just stand there with my hands behind my back wearing a hard hat,” Hirvonen laughs.
Yara’s project manager Mikko Lappalainen also appreciates the smooth installation. It did not require much of his attention, so he was able to focus on other projects.
“All in all, the design and implementation of the modernisation took our wishes and perspectives into account excellently. We worked together to find a suitable implementation solution. Of course, our operating environment and working methods are familiar to Simetek, who helped in the matter.”
“Simetek provided excellent mechanical engineering”
Anssi Pietarinen explains the background to the investment, which was that the old equipment had reached the end of its service life. Maintenance costs had risen so high that Yara decided it would be sensible to invest in a new conveyor to replace the old one. Increasing reliability and safety, and reducing maintenance costs were also contributing factors to the decision.
Yara also wanted to add frequency converters to the conveyor, which would enable the specification of the belt speed. They would also help to move away from fluid couplings. The frequency converters also meant that it was easier to service the equipment and, if necessary, the conveyor’s capacity can be raised by increasing the belt speed.
Simetek handled the mechanical engineering of the conveyor excellently. We were pleased with the technical solution they offered. It was a plus that they have a machine shop and design department all under the same roof. That makes service more cost-efficient and transparent towards the customer. “We always know what’s going on and where we are,” says Pietarinen.
He also appreciates that Simetek is able to handle the entire chain without subcontracting. The machine shop can handle machining, welding, edging, and, if necessary, flame-cutting. Pietarinen says that Simetek’s own installation engineers and foremen bring cost-efficiency, high quality, and safety to installations.
“The project progressed on schedule. We made small detail changes during the installation, but they were also a success. The collaboration between Simetek and the electrical contractor was also seamless. We were able to test run the equipment on schedule. The entire project was delivered excellently,” says Pietarinen.
He is also satisfied that Simetek always submits quotes on time and that they correspond to the request for a quote. They are well-prepared.
“Simetek has been a good supplier to us, and it is close by. They can be here half an hour after calling them, if necessary. That brings flexibility and efficiency to our work. We can get little things moving quickly,” adds Pietarinen.