The manufacture of railroad wagon unloading equipment at Mussalo Harbour for Oy M. Rauanheimo Ab has progressed to the installation stage. Over the last two weeks, Simetek’s team installed two elevators, two belt conveyors, a wagon unloading cone and railroad support steel structures. In addition, we removed the old unloading cone from the old conveyor and relocated the old conveyor.
“The installation has progressed well. No significant problems have been encountered, and the equipment have fitted well. The customer has been satisfied with the end results, and occupational safety has been taken care of in compliance with the regulations,” comments Pasi Knuuttila, Design Manager.
The installation at Mussalo Harbour continues with work on service levels and sealing. During the next two weeks, we will position the belt conveyor elevator.
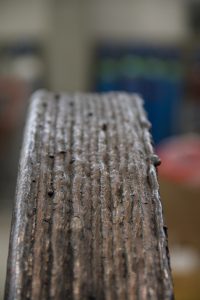
The hard facing method is selected based on the wear mechanism of the end product.
Hard facing is applied to parts that are subject to heavy abrasive wear. For example, in the mining industry, hard facing is used to protect products that convey ore.
“The most significant benefit achieved with hard facing is wear resistance. Longer product life enables longer service shutdown intervals, for example. The application of hard facing to a product ensures carefree usability,” says Aki Karvonen, Production Manager at Simetek.
Products welded using conventional materials have to be serviced and replaced often if they are subjected to heavy wear. When the production and installation of a new product can be avoided, the customer saves both costs and time.
In addition to abrasion, other types of wear may include so-called adhesive wear, which is caused by the movement of two metal parts against each other, impact wear and wear caused by high temperatures or corrosion. Specific hard facing methods have been developed for each of these wear mechanisms to improve the wear resistance of the product.
Suitable for repair welding
Hard facing can also be applied to heavy-wear areas in products that were originally welded using conventional materials. The application of hard facing can be done on the spot or at our machine shop if the product can be easily detached.
“Although most hard facing tools are also used when working with conventional materials, some materials require specialised tools. The method places certain special demands on welding,” explains Karvonen.
In comparison to conventional welding, the most remarkable difference is the use of a different filler. The fillers used in hard facing have been designed for this purpose only. The special alloy forms wear-resistant carbides in the finished weld. The carbides are usually either chromium or wolfram carbides.
Special skills required
As the material selection of hard facing fillers is extensive, hard facing requires special competence. The welder must know which filler to use with each product and how to use it to ensure that the product withstands its demanding operating conditions.
“Not many welders have the competence for hard facing. Thus, Simetek has provided in-house training to welders to ensure that its workforce have the know-how to select the right filler and work method,” Karvonen says.
Simetek Works Oy has applied hard facing in the manufacture and repair of various kinds of mining process equipment. The method is widely applied to heavy-wear products used in the forest industry as well.
Contact us!
“Simetek excels in the delivery of functional turnkey solutions.”
Pasi Knuuttila, Design Manager, started in his position at Simetek in 2016. He moved to the company from Tech Point Oy where his duties included the design of robot and automation cells. At Simetek, Knuuttila is responsible for mechanical design and design development, and he leads the design team.
“In addition, my responsibilities include the design of load-bearing steel structures and the sales and project design of larger turnkey projects,” says Knuuttila.
Knuuttila also participates in marketing and tender calculation activities and ensures that Simetek’s IT systems remain up and running. He considers problem-solving one of his strengths and gives praise to his reliable design team who, for their part, assist him in finding solutions to issues.
Knuuttila holds a Bachelor of Engineering degree in Mechanical Engineering. His experience includes working in the roles of foreman and mechanic at construction sites involving steel structures as well as in the role of maintenance foreman in various factories around Finland.
“The fact that I’m also a qualified mechanic and welder gives me helpful perspectives to the design work.”
Project of a larger scale
Knuuttila considers the manufacture of Mussalo Harbour railroad wagon unloading equipment for Oy M. Rauanheimo Ab one of the most interesting projects that Simetek currently participates in. Based on the scale and challenging nature of the project, it is among the most remarkable projects Simetek has carried out.
“Each link in Simetek’s supply chain participates in the implementation of the railroad wagon unloading equipment: from layout to sales and tendering, from design to manufacture at the machine shop and finally to the deployment of the automation system.”
According to Knuuttila, Simetek’s strengths include functional turnkey deliveries and the company’s security of supply.
Contact Pasi Knuuttila:
Pasi Knuuttila
Design Manger
Mechanical design
tel. +358 40 3533 260
Simetek has made preparations for the installation, disassembly and maintenance services that will take place during annual shutdowns in the summer.
Simetek applied hard facing to a rotary feeder rotor.
Simetek serviced an industrial gearbox to be placed in the customer’s storage.
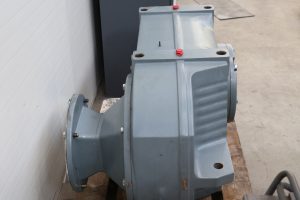
Simetek manufactured two mass boiler bottom covers from Duplex steel for Andritz Oy.
The design of Mussalo Harbour railroad wagon unloading equipment for Oy M. Rauanheimo Ab has been initiated.
Simetek machined a mining machine drill bit.

Simetek manufactured a leader from STRENX 700 high-strength for Junttan.