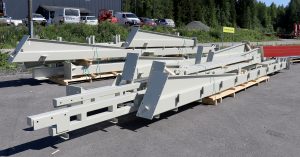
We designed and manufactured a shelter to protect railroad wagon unloading equipment at Mussalo Harbour as a turnkey delivery for Oy Rauanheimo Ab. The shelter will be covered with sheet metal and lighting and electrical installations will be added.
Read more about the project at Mussalo Harbour: https://simetek.com/2020/05/15/installation-stage-reached-at-the-mussalo-harbour-project-site/?lang=en
We welded, machined, and added bearings to a conveyor draw-in roller for Yara Suomi Oy’s warehouse.
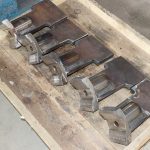
We welded and machined mixer blades for Agnico Eagle Finland.
We manufactured a feeding roll for our client.
We renovated a conveyor draw-in drum for Yara Suomi Oy.
Simetek manufactured a distribution flap from acidproof material for Yara Siilinjärvi.

Simetek manufactured and installed a railroad wagon unloading cone for Oy M. Rauanheimo Ab in the Mussalo Harbour.
When the equipment have been deployed, fertiliser loads transported by train are unloaded into the cone, after which the loads are transported to an elevator using a belt conveyor. The elevator lifts the loads to an existing conveyor.
Simetek designed, manufactured and installed the system’s train wagon unloading cone, belt conveyors, elevators and collector cones.
Read more about the Mussalo Harbour project: https://simetek.com/2020/05/15/installation-stage-reached-at-the-mussalo-harbour-project-site/?lang=en
“At Simetek, challenges are resolved jointly”
Ville Kinnunen, Project Manager at Simetek, is responsible for supervising projects and installation activities. Kinnunen gathered experience in installation work in his previous job at Yara Suomi Oy from which he moved to Simetek in early 2017.
Kinnunen’s job description involves versatile tasks from the supervision of installation to general project management. In addition, he is responsible for the procurement of raw and other materials as well as general scheduling and organising of duties. In addition, Kinnunen supports the design team as much as he can.
“I don’t participate in drawing blueprints, but if I come up with ideas concerning the implementation of plans, I can help and possibly offer alternative solutions.”
Kinnunen’s special responsibilities also include the supervision of session work. The projects he has enjoyed the most at Simetek include larger commissions in which he participated right from the start. He considers the opportunity to do new things the most interesting aspect of his job.
Kinnunen states that it is difficult to choose the single most challenging project, but in general, sudden changes to plans or timeframes may cause difficulties, especially if they require immediate action on the spot. At Simetek, any problems faced are solved jointly.
“For example, if the problem relates to hardware, that is, if a certain component doesn’t fit, we take a look at the issue with the design team to figure out what went wrong and how the situation can be resolved. Then a fitting component is manufactured at the machine shop, and the installation team fits it to its place. Challenges are resolved through cooperation,” states Kinnunen.
In his free time, Kinnunen engages in outdoor activities with his family and dog and spends time at his summer cabin. His family consists of his wife, two children and a Bernese mountain dog.

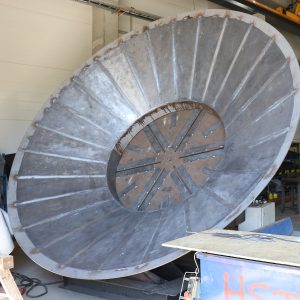
Simetek manufactured a bottom cone wet electrostatic precipitator to be used at Yara Suomi Oy’s sulphuric acid factory in Siilinjärvi. The current precipitator is repaired by replacing the worn-out bottom cone with a new one. The equipment’s wear resistance was improved by lining the cone’s inner surface with lead plates.
The project was ordered based on the customer’s needs. Simetek’s experts visited the site and initiated the project planning. The customer had already carried out the required imaging.
After material acquisition, we started to manufacture the cone at Simetek’s machine shop using black steel (S355J2G3). The manufacturing process involved sheet metal cutting, edging, sheet rolling and assembly welding. One bolt flange was also fitted into the cone in connection with flame cutting prior to the assembly welding.
“When other stages of the assembly were complete, we started lining the cone’s inner surface with lead,” explains Ville Kinnunen, Project Manager at Simetek.
Lead burning improves load and wear resistance
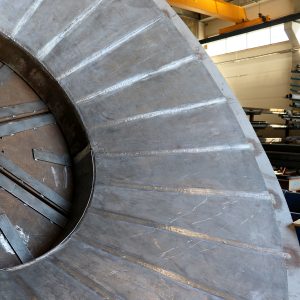
The cone was lined with lead for several reasons. First of all, the device into which the bottom cone would be placed was originally lined with lead on the inside. Lead burning enabled consistency between the new and the old cone.
According to Kinnunen, lead burning improves the cone’s resistance to loads and wear in comparison to plastic or glass fibre linings which are also used in corresponding applications. In Yara’s case, the low pH value and relatively high flow rate of the sulphuric acid place demanding requirements for the special protection of the device.
“Moreover, lead is a less expensive alternative than special steels that are also used in heavy-wear applications. From the perspective of cost-efficiency, lead lining is the best option.”
The machine shop stage of the project took only approximately two weeks. Lead lining, on the other hand, is remarkably slower. Kinnunen estimates that the lead burning of Yara’s cone requires approximately one month of work from a pair of workers.
Following the cone manufacture, Yara also ordered the cone’s installation which will be implemented in connection with the factory’s annual maintenance in autumn 2020.
Read more about our lead burning services!
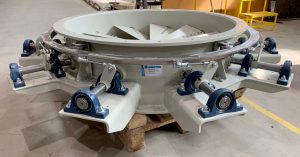
Simetek manufactured a blower blade controller for Yara Suomi Oy. The delivery also included product design.