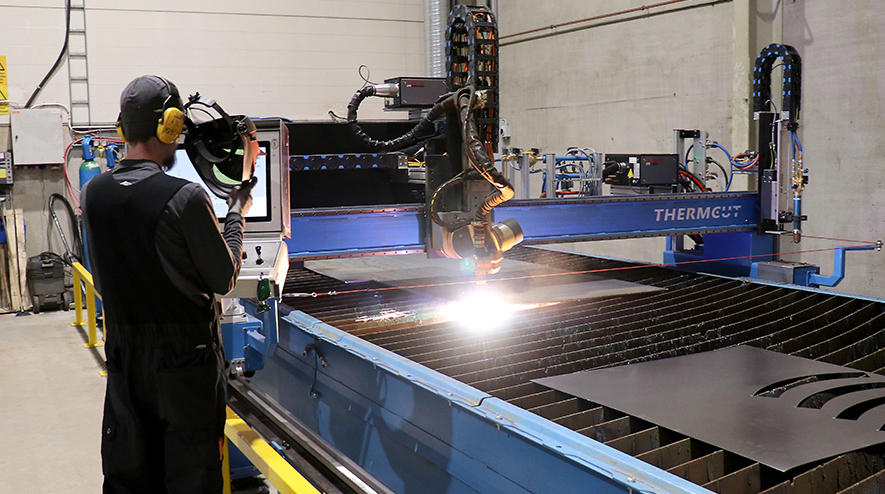
We improved its operational efficiency with a development project
Undertaking a three-year development project, we used the Lean manufacturing model to improve the operations of our workshop. We redesigned the production space layout: machines were repositioned and the storage area and goods entrance moved to another location. We also purchased new equipment and updated our safety.
Supported by the European Regional Development Fund (ERDF), we started the development project in December 2020 and completed it in August 2023. The aim of the project was to determine the optimal flow of materials during production. For example, one measure was to increase the flow by purchasing a 300 square meter outdoor storage hall for intermediate storage. The hall allows us to keep equipment, steel, parts sent in by customers for refurbishment, and even finished parts away from the weather.
We also upgraded the lighting in our production facilities. Old sodium lamps were replaced with LEDs, which both save energy and improve safety, thanks to their increased luminosity. We also gave every tool a marked spot to improve workflow.
Cutting machine adds flexibility to production
Our largest investment was a fine plasma cutter, now two years old, that allows us to make our own cuts instead of relying on and scheduling ourselves according to subcontractors. According to managing director Timo Roivainen, the plasma cutter was an essential investment that has introduced flexibility to our production.
“The cutter has been a great boon to us. In recent times, Covid and the war in Ukraine would have pushed our deliveries back by several weeks if we didn’t have our own cutter. Now we’ve been able to quickly respond to customer needs,” says Roivainen.
In conjunction with the plasma cutter, we also upgraded our air compressor and dust removal and manufactured a deburring machine. The deburring machine smoothes the edges of pieces for welding.
Other purchases include a parts washer, turn table for mechanised welding, modern pulsed arc welder for difficult welds, titanium welding set, and modifications to our trimming press.
Upgrades to the paint shop and blast room
During the project, we made improvements to the paint shop’s workflow to remove the need to move pieces against the flow. We also added an extra entry point, which has proven so useful that managing director Roivainen says it should have been built 20 years ago.
“We also purchased 2K spray painting equipment for the paint shop. With this modern equipment, we want to increase safety and reduce paint waste. We’ve also seen a reduction in breakdowns. Our old pumps were more liable to malfunction if they weren’t cleaned to perfection. The new equipment is self-cleaning,” says Roivainen.
The blast room walls were coated with polyurethane during the project to do away with protective sheets. This change made the room more spacious and comfortable, and it also avoids the need to replace the sheets.
Operational improvements continue
The scale of the development project was over half a million euros, some of which came from the ERDF. The funding was welcome, even though we were required to pay for most of the project ourselves.
According to Roivainen, the effects of the project are difficult to estimate in terms of money, but it has improved employee satisfaction and safety. The flow of production has also improved considerably.
“We improve our operations continuously, and that work continues after the end of the project,” says Roivainen.
Simetek customers include major industrial players such as Yara Suomi Oy, Andritz Oy, Kraton Chemical Oy, Agnico Eagle Finland Oy, and Oy M. Rauanheimo Ab.