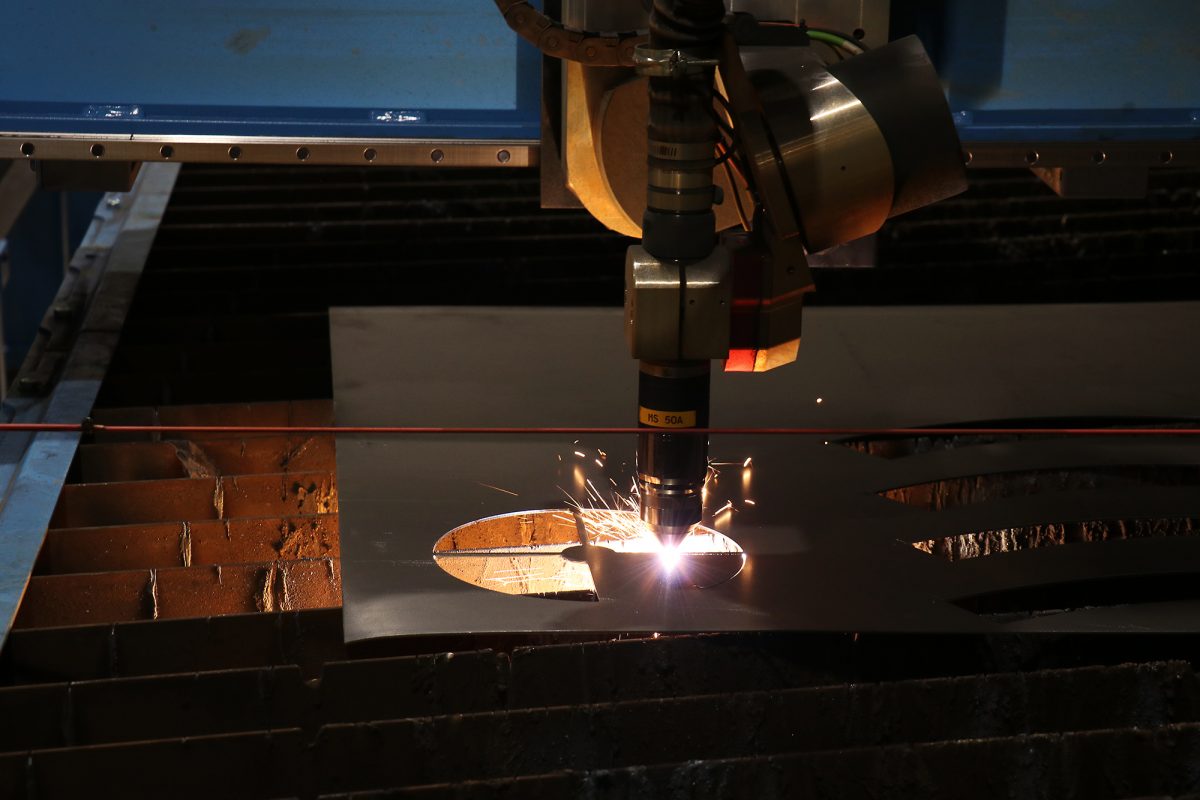
A fine-particle plasma cutting machine boosts Simetek’s production
Last year, Simetek purchased a new fine-particle plasma cutting machine (Thermcut CD3500), which is used to cut steels that are sent for further processing in machining and welding – or are sent directly as cuts to the customer. The procurement of the machine relates to a significant development project that is under way in the machine shop.
The procured machine combines the functionalities of a flame-cutter and a fine-particle plasma cutter in the same package. Flame-cutting is used to cut thicker structural steel sheets and wear plates. Fine-particle plasma meanwhile is able to cut thinner structural steel sheets at a faster cutting speed than is possible using flame-cutting. In addition, plasma can be used to cut stainless and armour steels, while flame-cutting cannot.
“The fine-particle plasma cutting machine uses various gases that it adjusts to cut sheets. This makes for a clean cut. The machine is also able to optimise the right cutting speed for each material and material strength. The flame-cutting console meanwhile uses oxygen and propane as cutting gases,” explains Simetek’s managing director Timo Roivainen.
Simetek’s own flame-cutting machine helps to anticipate work phases
The flame-cutting machine can be used to cut 150 mm thick sheets, while the plasma-cutter is limited to around 45 mm for stainless steel and around 60 mm for black steel. The largest sheet that can be cut is 2500 x 6000 mm. Simetek’s sheeting warehouse currently covers structural steel sheeting of 1–80 mm and acid-resistant sheeting of 1–35 mm, plus a large number of other special steels. The warehouse is stocked based on supply and demand.
The machine also has an angle cut feature, which indirectly also affects cleanliness and safety. The feature helps to avoid grinding and machining angles. This keeps the production facilities cleaner and improves ergonomics for welders.
The fine-particle plasma cutter is CNC-controlled and connected to the machine shop’s network. The foreman makes the cutting programs on the machine. In practice, they place the cuts on the sheet and the sheets then progress to cutting. The machine has a marking feature which allows you to add your own edge markings and threaded hole markings.
“The machine makes our production more efficient: its cutting speeds are modern, and we know precisely when the cuts are ready for the next work phase. The machine allows us to respond to customers’ urgent needs,” says Roivainen.